Table of Content
If you are committed to making glass blowing your career, you can take the studio to your home. Using your mouth, carefully begin to blow air through the cool end of the pipe until the glass is expanded to the size you want. When you have your first layer of glass gathered on, you should make sure to keep the pipe rotating at all times. Warming the tip of the pipe before gathering will allow the molten glass to go onto the pipe evenly, without any bubbles. Master gaffers have a huge array of equipment in their studios with them, to help them with diverse and challenging projects.
Then, remove the glass periodically and mix it to remove bubbles. You can also pour your molten glass into a mold to shape it. Finally, when you're ready, cool your glass in your kiln, which is known as annealing.
What is fusing?
Alternatively, find a small glass panel from a craft or hardware store, but avoid traditional window glass as it’s often too large to easily paint. Pick thick water-based glass paint if you’d like to be able to peel your art off the glass and end up with a transparent painting. Select acrylic paint if you’d like a non-toxic, opaque paint that’s easy to clean up and apply.

Keep in mind that two layers are best, and design something to suit. If you love stained glass objects, you could have a go at making them yourself. The craft of stained glass is not difficult to learn, as long as you follow the instructions, take all proper precautions, and put in enough practice.
Preparing to Fuse
Anyhow, not having any clue as to when this design instruction was created I may be writing to the wind. But as I plan on going thru all the steps, and being a talkative sorta bloke, I'll take the opportunity to comment as we go. Finally, clean your piece well with a mild detergent or glass cleaner, and display in a well-lit environment. To hang the piece, I soldered on two loops of tinned copper wire . This was plenty of strength to hold the weight of this piece.
Smooth the foil tape with your fingers and then burnish with the lathekin. Once you have foiled all the pieces, assemble them together once more. Have you always cherished a desire to make stained glass? This article will help you with some easy steps to make it at home. This method will push a conventional barbecue past its normal temperature limits - so hot that it's even possible to melt the grill itself.
Leaded Stained Glass Artistry
Fortunately, there are many stores offering art glass supplies such as fused art glass, bullseye glass, CBS Dichroic, glass stringers, and jewelry embellishments. There’s also many different creative things you can do. You can mix big shapes with small bits of glass frit. There’s gold mica powders, decals and iridescent surfaces. You can create bubbles, add wire, use stencils.
These are just the very basic steps of stained glass making. With practice and more research in the subject, you can refine your skills and create some spectacular effects. It's possible if you're using regular beach sand with impurities instead of pure silica sand. If this is the case, you can use a mask and avoid standing close to the kiln while melting the glass. The molten glass can be poured into a bath of molten tin for support and blasted with pressurized nitrogen to shape and polish it.
.By using this service, some information may be shared with YouTube.
Aluminum oxide or silica carbide can be typical grit mediums often used in sandblasting glass. This can create the same effect as acid etching. I tend to use this method for my work because I have better control… And it is much safer than acid etching. Kiln casting glass can involve hot molten glass poured into a mold inside the kiln. Casting with molds in a kiln includes using crushed glass or a powdery glass paste known as ‘pate de verre‘. The only hard part would be cutting the long stem.
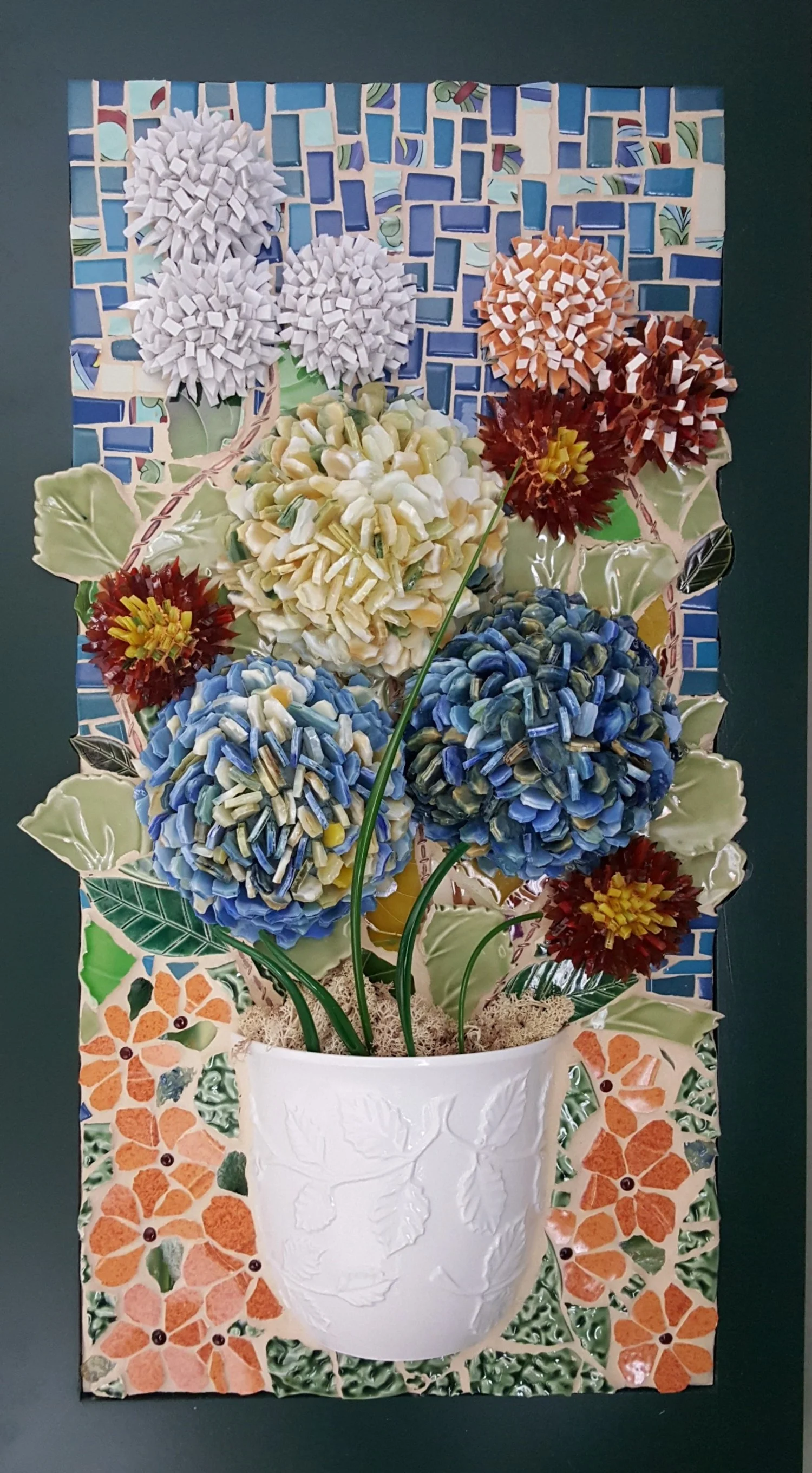
Set your glass and the mold on the kiln shelf and place it back in the kiln. Consult your kiln manual and program the kiln to reach around 1225 degrees Fahrenheit . Let the kiln cool completely before you remove your glass. The art of fusing different glasses together can be used to create sculptures, jewelry, dishware, and other beautiful pieces. Despite the intricate appearance of fused glass, the process of fusing glass together is quite simple. With the right tools and safety gear you can learn how to fuse glass into dazzling works of art.
Creating stained glass objects requires some skill and precision, but can be a fun project. Soul Ceramics is an online retailer providing the lowest online prices for ceramics and pottery equipment, heat treating ovens, glass fusing kilns and other art supplies. There is specific glass used for glass fusing which is called ‘fusible glass’. The best thickness for fused glass at home is 1/4inch .

Cover the edges of the glass with the copper foil, then paint a layer of flux on the foil. Use the solder and soldering iron to attach the pieces of foiled glass together, following your template. When you’re done, you can frame your piece in a zinc frame or lead channel. You’ll need to solder the pane of glass into the frame. Copper Foil - Some stained glass works use lead came, which is a lead channel that holds pieces of glass together. This is a completely different technique than I am showing you.
When you’re working with glass and chemicals, it is only sensible to take all possible precautions. A little care and attention will prevent accidents and you can have an enjoyable crafting experience. So, firstly, get a studio or set aside a room in your home for your work.

No comments:
Post a Comment